樹脂灌注成型工藝(Resin Transfer Molding——RTM)是從濕法鋪層和注塑工藝演變而來的一種新的復合材料成型工藝,RTM的技術(shù)起源,有資料認為是起源于20世紀40年代的“MARCO”方法。初期開發(fā)的技術(shù)主要在歐洲,在60年代至70年代,玻璃鋼領(lǐng)域?qū)⒅攸c放在噴射和片狀模塑料成型上,RTM雖然成本較低,但其技術(shù)要求較高,特別是對原材料及模具的要求較高,大規(guī)模推廣有一定的困難,因而發(fā)展緩慢。到了20世紀80年代,由于工業(yè)發(fā)達國家對生產(chǎn)環(huán)境要求的各項法規(guī)日趨嚴格,如美國、英國對工作區(qū)苯乙烯的限量濃度為100×10-6,北歐和日本限量濃度為50×10-6等,為此,生產(chǎn)廠家不得不放棄傳統(tǒng)的手糊和噴射成型工藝,尋找符合環(huán)保法規(guī)的低苯乙烯揮發(fā)量的工藝。同時,隨著原材、工藝的發(fā)展和成型技術(shù)的不斷進步,加上RTM工藝自身諸多的優(yōu)點,如模制件公差小,有很高的表面質(zhì)量,與SMC比較模塑壓力小,生產(chǎn)加工組織方式多種多樣,投資少,生產(chǎn)效率較高等特點而受到各國的重視。 1985年前后,以縮短成型周期、提高表面質(zhì)量平順性和提高質(zhì)量穩(wěn)定性為目標的第二代RTM開始得到應用。第二代RTM的典型特征是使用中溫固化體系,纖維使用預成型的方式,生產(chǎn)效率得到大幅度提高,單模生產(chǎn)周期縮短到20~30分鐘,真空輔助成型得到了普遍應用。以更高效率為特點的第三代RTM工藝在20世紀90年代中期開始得到應用,聚酯類樹脂的成型溫度提升到120℃以上,成型效率達到了單模生產(chǎn)5分鐘。代表性的產(chǎn)品有法國Sortira公司為福特生產(chǎn)的轎車擾流板,日產(chǎn)量可以達到800件,生產(chǎn)效率完全可以和SMC相比。 RTM工藝一個重要發(fā)展方向是大型部件的整體成型。工藝方法以VARTM、Light-RTM、SCRIMP工藝為代表,主要應用于汽車、船艇、風機葉片等大型或者特大型部件的整體成型。進入21世紀以后,RTM工藝在大型結(jié)構(gòu)部件的制造中表現(xiàn)出了明顯的優(yōu)勢,在各領(lǐng)域得到了越來越多應用。 國內(nèi)的RTM工藝的起步于20世紀80年代末期,受當時國際RTM技術(shù)高速發(fā)展的影響,一些中小型企業(yè)基于想改變傳統(tǒng)手工操作局面的想法,引進了許多RTM注射設(shè)備,一度形成“熱點”。但是由于受當時原材料配套系統(tǒng)的不完善和基礎(chǔ)工藝理論研究欠缺的影響,未能形成規(guī)?;a(chǎn),大部分設(shè)備都處于閑置狀態(tài)。20世紀90年代以后,國內(nèi)一些單位積極研究和推廣RTM工藝技術(shù),從原材料、產(chǎn)品設(shè)計、模具設(shè)計與制造、A級表面技術(shù)和基礎(chǔ)理論以及工業(yè)化生產(chǎn)技術(shù)等方面,開展了系統(tǒng)的研究工作。期間比較有代表性的產(chǎn)品在民用領(lǐng)域有富康轎車背門、奧拓轎車尾翼、座椅、電話亭等產(chǎn)品。進入21世紀后,隨著三維編織技術(shù)的快速發(fā)展,RTM在飛機部件和其它軍用產(chǎn)品上得到了較多的應用,而隨著Light-RTM 和SCRIMP在游艇和風機葉片上的應用,該類型工藝的應用優(yōu)勢越來越多地得到了大家的認可和熟悉。 RTM工藝技術(shù)的研究和應用涉及材料學、流體力學、化學、計算機模擬仿真及實時監(jiān)控技術(shù)等諸多交叉學科領(lǐng)域,是當前國際復合材料最活躍的研究領(lǐng)域之一。其主要研究方向包括:低黏度高性能樹脂體系的制備及其化學動力學和流變特性;纖維預成型體的制備及滲透特性;成型過程的計算機模擬仿真技術(shù);成型過程的在線監(jiān)控技術(shù);模具優(yōu)化設(shè)計技術(shù);新型工藝設(shè)備的開發(fā);成本分析技術(shù)等。 RTM以其優(yōu)異的工藝性能,已廣泛地應用于艦船、軍事設(shè)施、國防工程、交通運輸、航空航天和民用工業(yè)等。其主要特點如下:(1)模具制造和材料選擇靈活性強,根據(jù)不同的生產(chǎn)規(guī)模,設(shè)備的變化也很靈活,制品產(chǎn)量在1,000-20,000之間,采用RTM成型工藝可獲得最佳生產(chǎn)經(jīng)濟效益。(2)能制造具有良好表面質(zhì)量、高尺寸精度的復雜部件,在大型部件的制造方面優(yōu)勢更為明顯。(3)易實現(xiàn)局部增強、夾芯結(jié)構(gòu);容易靈活調(diào)整增強材料的類型、結(jié)構(gòu)設(shè)計,以滿足從民用到航空航天工業(yè)不同性能的要求。(5)RTM成型工藝屬一種閉模操作工藝,工作環(huán)境清潔,成型過程苯乙烯排放量小,有利于環(huán)保。(6)RTM成型工藝對原材料體系要求嚴格,要求增強材料具有良好的耐樹脂流動沖刷和良好的浸潤性,要求樹脂黏度低,高反應活性,中溫固化,固化放熱峰值低,浸漬過程中黏度較小,注射完畢后能很快凝膠。(7)低壓注射,一般注射壓力<30psi,可采用玻璃鋼模具(包括環(huán)氧模具、玻璃鋼表面鑄鎳模具等),鋁模具等,模具設(shè)計自由度高,模具成本較低。 與預浸料模壓工藝相比,RTM工藝無需制備、運輸、儲藏冷凍的預浸料,無需繁雜的手工鋪層和真空袋壓過程,也無需熱處理時間,操作簡單。技術(shù)的開發(fā)和擴大應用之所以活躍,主要是因為其工藝過程前期樹脂和纖維相對分離,纖維材料的組合自由度非常大,不同類型的纖維以及不同結(jié)構(gòu)形式的編織方法都可以應用,多種類型的樹脂也可以根據(jù)產(chǎn)品需要來選擇。 但是RTM工藝由于在成型階段樹脂和纖維才通過浸漬過程實現(xiàn)賦型,纖維在模腔中的流動、纖維浸漬過程以及樹脂的固化過程都對最終產(chǎn)品的性能有很大的影響,因而導致了工藝的復雜性和不可控性增大。表6-1列出了手糊、RTM、SMC/BMC成型方法適用性的比較。
比較 | 手糊 | RTM | SMC/BMC |
生產(chǎn)規(guī)模 (件/年) | 小于1000 | 5,000-10,000 | 10,000以上 |
模塑溫度 | 室溫 | 40-60℃(室溫也可以) | 130-150℃ |
成型周期 | 1-4h | 5-30min | 1-15min |
生產(chǎn)效率/8h | 2-3 | 16-90 | 50-400 |
模具類型 | FRP | FRP或金屬 | 金屬 |
模具費(以開模為1) | 1 | 2-4 | 5-10 |
制品表面效果 | 一面光 | 兩面光 | 兩面光 |
部件重復性 | 人為因素影響較大 | 較好 | 很好 |
部件尺寸精度 | 人為因素影響較大 | 較好 | 很好 |
樹脂、纖維比例 | 人為因素影響較大 | 較好 | 很好 |
填料含量 | 高 | 較低 | 高 |
脫模劑 | 外脫模 | 內(nèi)外都可 | 內(nèi)脫模 |
壓力 | 接觸壓力 | 0.1-0.25 MPa | 4-10MPa |
RTM工藝的基本原理如圖6-1所示,先在模腔內(nèi)預先鋪放增強材料預成型體、芯材和預埋件,然后在壓力或真空作用力下將樹脂注入閉合模腔,浸潤纖維,固化后脫模,再進行二次加工等后處理工序。
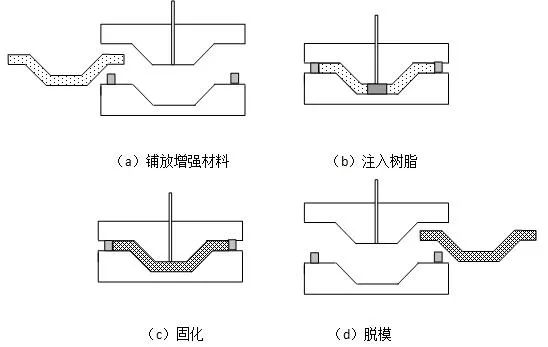
纖維預成型有手工鋪放、手工纖維鋪層加模具熱壓預成型、機械手噴射短切加熱壓預成型、三維立體編織等多種形式,需要達到的效果就是纖維能夠相對均勻填充模腔,以利于接下來的樹脂充模過程。 在合模和鎖緊模具的過程中,根據(jù)不同的生產(chǎn)形式,有的鎖模機構(gòu)安裝在模具上,有的采用外置的合模鎖緊設(shè)備,也可以在鎖緊模具的同時利用真空輔助來提供鎖緊力,模具抽真空同時可以降低樹脂充模產(chǎn)生的內(nèi)壓對模具變型的影響。 在樹脂注入階段,要求樹脂的黏度盡量不要發(fā)生變化,以保證樹脂在模腔內(nèi)的均勻流動和充分浸漬。在充模過程結(jié)束后,要求模具內(nèi)各部分的樹脂能夠同步固化,以降低由于固化產(chǎn)生的熱應力對產(chǎn)品變形的影響。這種工藝特點對于樹脂的黏度和固化反應過程以及相應的固化體系都提出了比較高的要求。 隨著原材料技術(shù)、模具技術(shù)、設(shè)備技術(shù)的快速發(fā)展,RTM的生產(chǎn)布局也出現(xiàn)了多種多樣的形式。 按照生產(chǎn)效率劃分,可以將RTM工藝的發(fā)展劃分為三代。第一代RTM工藝通常為常溫固化或外部加熱,生產(chǎn)周期在80~150分鐘左右,其生產(chǎn)布局如圖6-2所示。生產(chǎn)布局常采用環(huán)形生產(chǎn)線,模具在不同的工位流動,模具數(shù)量多,生產(chǎn)周期取決于時間最長的工序, 通常為固化工序。圖6-2 RTM環(huán)形生產(chǎn)線
第二代RTM工藝的特點是模具自帶加熱系統(tǒng),同時采用了專門的開合模鎖緊機構(gòu),生產(chǎn)效率可以達到20~30 分鐘。圖6-3所表示的是代表性的雙工位RTM工藝布局,一個工位在噴射膠衣、鋪放纖維時,另一個工位可以進行注射、固化過程。
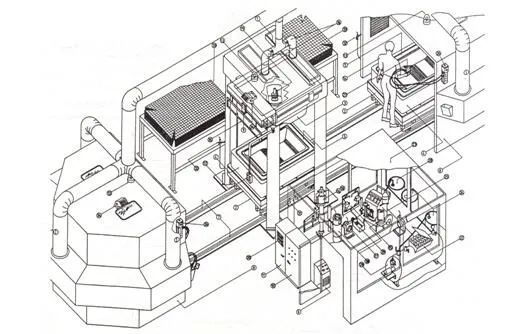
第三代RTM工藝采用的是120℃左右的固化溫度,模具由專用的壓機帶動實現(xiàn)開模、合模、鎖緊,設(shè)備采用高速注射設(shè)備,模具使用金屬模具,整體布局和SMC工藝類似,成型周期小于10分鐘。如圖6-4所示。
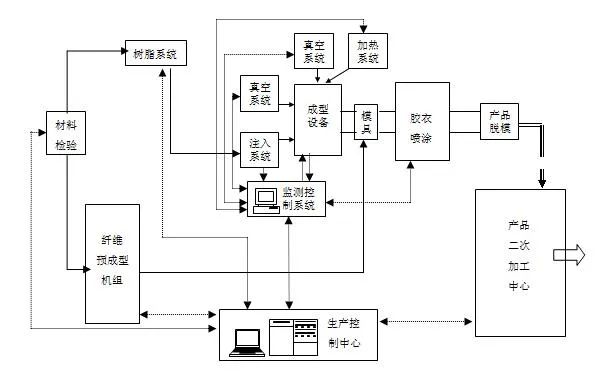
圖6-4 第三代RTM工藝自動化生產(chǎn)線布局 影響RTM工藝的工藝參數(shù)包括樹脂黏度、注射壓力、成型溫度、真空度等,同時這些參數(shù)在成型過程中是互相關(guān)聯(lián)和互相影響的。 (1) 樹脂黏度 適用與RTM工藝的樹脂應該具有較低的黏度,通常應小于600mPa?s,小于300mPa?s時工藝性會表現(xiàn)地更好。當所使用的樹脂黏度較高時通常提高樹脂和成型溫度來降低樹脂黏度,以利于更好地實現(xiàn)充模過程。 (2) 注射壓力 注射壓力的選擇取決于纖維的結(jié)構(gòu)形式和纖維含量以及所需要的成型周期。很多的研究資料都表明,較低的注射壓力有利于纖維的充分浸漬,有利于力學性能的提高。通過改變產(chǎn)品結(jié)構(gòu)設(shè)計、纖維鋪層設(shè)計、降低樹脂黏度、優(yōu)化注射口和排氣口的位置、使用真空輔助等手段,都可以實現(xiàn)降低注射壓力。 (3) 成型溫度 成型溫度的選擇受模具自身能夠提供的加熱方式、樹脂固化特性及所使用的固化體系的影響。較高的成型溫度能夠降低樹脂的黏度,促進樹脂在纖維束內(nèi)部的流動和浸漬,增強樹脂和纖維的界面結(jié)合能力。有資料數(shù)據(jù)顯示,較高的溫度能夠提高產(chǎn)品的拉伸強度。 (4) 真空度 在成型過程中使用真空輔助可以有效降低模具的剛度需求,同時促進注射過程中空氣的排除,減少產(chǎn)品的孔隙含量。通過實驗數(shù)據(jù)測定,在真空條件下成型的平板平均孔隙含量只有0.15%,而沒有真空的平板孔隙含量達到1%。 隨著應用領(lǐng)域的不斷擴大,RTM工藝已經(jīng)發(fā)展出了一系列的衍生工藝,代表性的工藝包括:Light-RTM、SCRIMP(Seemann Composites Resin Infusion Molding Process)、RFI(Resin film infusion)等。 Light-RTM通常稱之為輕質(zhì)RTM,該工藝是在真空輔助RTM工藝的基礎(chǔ)上發(fā)展而來的。適用于制造大面積薄壁產(chǎn)品。該工藝的典型特征是下模為剛性模具,而上模采用輕質(zhì)、半剛性的模具,通常厚度在6~8毫米。工藝過程使用雙重密封結(jié)構(gòu),外圈真空用來鎖緊模具,內(nèi)圈真空導入樹脂。注射口通常為帶有流道的線型注射方式,有利于快速充模。由于上模采用了半剛性的模具,模具成本大大降低,同時在制造大面積的薄壁產(chǎn)品時,模具鎖緊力由大氣壓提供,保證了模具的加壓均勻性,模制產(chǎn)品的壁厚均勻性非常好。 SCRIMP成型技術(shù)是由美國西曼復合材料公司在美國獲得專利權(quán)的真空樹脂注入技術(shù)。與之類似的工藝有多種,但名稱各不相同,以SCRIMP工藝最有代表性。其工藝原理是:在真空狀態(tài)下排除纖維增強體中的氣體,通過樹脂的流動、滲透,實現(xiàn)對纖維的浸漬。成型模具首先將一層或幾層纖維織物鋪放于模具上,再放好各種輔助材料,然后用真空袋密封,開啟樹脂閥門吸注膠液,充滿模具最后固化成型。 與傳統(tǒng)的RTM工藝相比,它只需一半模具和一個彈性真空袋,這樣可以節(jié)省一半的模具成本,成型設(shè)備簡單。由于真空袋的作用,在纖維周圍形成真空,可提高樹脂的浸濕速度和浸透程度。與RTM工藝相反,它只需在大氣壓下浸漬、固化;真空壓力與大氣壓之差為樹脂注入提供推動力,從而縮短成型時間。浸漬主要通過厚度方向的流動來實現(xiàn),所以可以浸漬厚而復雜的層合結(jié)構(gòu),甚至含有芯子、嵌件、加筋件和緊固件的結(jié)構(gòu)也可一次注入成型。SCRIMP工藝適用于中、大型復合材料構(gòu)件,施工安全、成本較低。 RFI首次是由L.Letterman(美國波音公司)申請的專利,最初是為成型飛機結(jié)構(gòu)件而發(fā)展起來的。近年來,這種技術(shù)已改進了RTM中纖維含量低、模具費用昂貴、易生成缺陷等缺點。RFI也是采用單模和真空袋來驅(qū)動浸漬過程。工藝過程是將預制好的樹脂膜鋪放在模具上,再鋪放纖維預成型體并用真空袋封閉模具;將模具置于烘箱或熱壓下加熱并抽真空,達到一定溫度后,樹脂膜熔融成為黏度很低的液體,在真空或外加壓力的作用下樹脂沿厚度方向逐步浸潤預成型體,完成樹脂的轉(zhuǎn)移;繼續(xù)升溫使樹脂固化,最終獲得復合材料制品。RFI工藝與現(xiàn)有的成型技術(shù)相比具有以下優(yōu)點: (1) 不需要復雜的樹脂浸漬過程,成型周期短,能一次浸漬超常厚度纖維層,具有高度三維結(jié)構(gòu)的縫編、機織預制件都能浸透,并可加入芯材一并成型; (2) 樹脂膜在室溫下有高的粘結(jié)性,可粘著彎曲面; (4) 模具制造與材料選擇的靈活性強,不需要龐大的成型設(shè)備就可以制造大型制件,設(shè)備和模具的投資低; (5) 成型產(chǎn)品孔隙率低(<0.1%),纖維含量高(重量含量接近70%),性能優(yōu)異。 RFI工藝也存在一些不足之處,如:對樹脂體系要求嚴格;不太適合成型形狀復雜的小型制件;由于采用真空袋壓法,制品表面受內(nèi)模的影響,達不到所需的復雜程度及精度要求;RFI工藝中,樹脂的用量不能精確計量,需要吸膠布等耗材除去多余樹脂,因而固體廢物較多。第三節(jié) 增強材料和纖維預成技術(shù) 在RTM模具中手工鋪放增強材料是一件比較困難的工序。在鋪放過程中,增強材料容易錯位,同時增強材料的變型不能夠與模具的型面變化相適應,需要手工剪開,然后粘接或縫合,這對于連續(xù)生產(chǎn)的一致性和效率都會產(chǎn)生影響。通過將纖維用一定的工藝手段預先制作成和模腔結(jié)構(gòu)一樣的預成型體,可以很好地解決這一問題。 RTM用的纖維類型包括E玻纖、R玻纖和S玻纖,以及各種高強高模碳纖維和芳綸纖維。所使用的玻璃纖維織物結(jié)構(gòu)形式包括表面氈、機織布、短切氈、連續(xù)氈、縫編氈、多軸向織物、RTM專用復合氈以及立體編織物等多種類型。碳纖維等高性能纖維通常使用不同織造方法的布,在很多高性能部件的制造場合,三維立體仿形織物的應用越來越多。 方格布是最為常見的機織布,其它類型的機織布如斜紋布、緞紋布等都可以用于RTM工藝。各種類型的機織布在鋪層時很容易發(fā)生皺折和扭曲,不容易鋪放到位。因此機織布通常用于一些型面變化比較簡單的產(chǎn)品,為保證纖維在模具內(nèi)的穩(wěn)定,可以使用特定的粘接劑固定織物,也可以采用手工縫編的方式,用滌綸線將布與布之間縫合在一起。 短切氈用于RTM工藝的優(yōu)點是成本低,變形性好,缺點是耐沖刷性差,但是如果在靠近模具注射口的短切氈上面鋪放機織布,可以降低樹脂對纖維的沖刷。從實際使用的情況來看,短切氈和機織布配合使用可以提高制品層間的剪切性能,同時實現(xiàn)纖維在不同分布方向上的互補。 玻璃纖維連續(xù)原絲氈是一種重要的玻纖無紡增強基材,它是以一定數(shù)量的連續(xù)玻纖原絲隨機分散成圈狀均勻分布于網(wǎng)帶上,靠原絲間互相交搭的連鎖作用及少量粘結(jié)劑結(jié)合成氈。連續(xù)氈的單位面積質(zhì)量為225~900g/m2,厚度為2~5毫米。由于連續(xù)氈具有各向同性、抗移性好、耐樹脂沖刷、貼覆性好、制品強度高等優(yōu)點,成為RTM工藝中非常重要的一種增強材料。 國外連續(xù)氈生產(chǎn)工藝主要采用“一步法”成氈技術(shù),即在玻璃池窯拉絲漏板下布置多臺成型工藝裝置,通過數(shù)臺拋絲機將纖維拉出并直接鋪撒在行進的網(wǎng)帶上形成氈坯,再經(jīng)過施膠、烘干,收卷成氈。這種工藝的特點是纖維分散性好,產(chǎn)量大,自動化程度高。目前國際上“一步法”成型生產(chǎn)工藝以美國歐文斯科寧公司和法國圣戈班公司為代表。 縫編氈是通過縫編機將不同的類型纖維縫合成纖維氈的結(jié)構(gòu)形式。縫編氈可以通過不同的縫合方式實行纖維織物多種增強結(jié)構(gòu)形式,是RTM工藝中應用最多、成本較低的一種增強材料。各種縫編氈的類型包括: (1)單軸向織物 僅在與織物長度方向0(經(jīng)向)或90(緯向)的一個方向平行鋪設(shè)無捻粗紗并縫合成織物。 (2)雙軸向織物 與織物長度方向成0、90、±45度的四個方向任意兩個方向平行鋪設(shè)無捻粗紗,每個方向各自形成獨立的紗層并縫合成雙軸向織物。 (3)多軸向織物 在與織物長度成0、90、±45的四個方向任意三個或四個方向上平行鋪設(shè)無捻粗紗,然后縫合成多軸向織物。 (4)縫編短切氈 用組合在縫編機上的短切機,將無捻粗紗短切并鋪撒均勻、然后縫合成氈。 (5)縫編復合氈 將單軸向織物、雙軸向織物、多軸向織物中的任意一種與縫編短切氈在縫編機上可縫合制成2~5層縫編復合氈。 三維編織是通過長短纖維相互交織而獲得的三維無縫合的完整結(jié)構(gòu),其工藝特點是能制造出規(guī)則形狀及異形實心體并可以使結(jié)構(gòu)件具有多功能性——即:編織多層整體構(gòu)件。三維織物主要應用于對力學性能要求非常高的航空航天結(jié)構(gòu)部件的制造。 編織工藝的原理是:由許多按同一方向排列的纖維卷通過紗線運載器精確地沿著預先確定的軌跡在平面上移動,使各纖維相互交叉或交織構(gòu)成網(wǎng)絡(luò)狀結(jié)構(gòu),最后打緊交織面而形成各種形態(tài)增強結(jié)構(gòu)的三維織物。 (1)異型件一次編織整體成型,實現(xiàn)了人們“直接對材料進行設(shè)計”的構(gòu)想; (2)結(jié)構(gòu)不分層,層間強度高,綜合力學性能好。 國外在纖維預成型體方面的研究、應用起步較早,涉及內(nèi)容已相當深入、全面,并針對產(chǎn)品性能、功能和用途要求建立了一系列相適應的預成型體制備方案。已經(jīng)研究開發(fā)的常用方法有三種:第一種方法是紡織、針織或編織凈外形或接近凈外形的預成型體;第二種方法是將增強材料縫合成彈性、半彈性的增強材料部件嵌入模具中;第三種方法是粘結(jié)預成型方法,對于某些具體的部件,它們常??梢元毩⒒蚧旌鲜褂谩@w維預成型技術(shù)在國外的工業(yè)產(chǎn)品中代表性的案例,如:Dowty航空公司用編織預成型方法成功生產(chǎn)了螺旋槳葉片;1987年美國福特四輪驅(qū)動轎車Aerostar橫梁、福特P100皮卡后擋板預成型體采用了CFRM熱沖壓成型等。目前國外許多研究者們?nèi)栽陬A成型體粘接劑、制備方法、粘接劑對工藝及制品性能的影響等方面開展研究工作,并且在預成型體設(shè)計,預成型體變形性,滲透性,力學性能分析等多方面建立了理論,并逐漸向數(shù)字模擬分析,力學性能預測和流變性能預測的方向發(fā)展。PAM公司成功開發(fā)了PAM-Form預成型體分析軟件,并做到與PAM-RTM的多物理場耦合分析,提高了復合材料制品性能的控制和預測能力。這些研究方向?qū)嶋H是RTM工藝和預成型體工藝工業(yè)化技術(shù)水平發(fā)展到目前的一種市場需求,反映了預成型技術(shù)在國外已經(jīng)從RTM工藝需要的附屬工藝流程中分離,逐漸形成一整套獨立的成型工藝過程。 預成型體必須滿足一系列的工藝要求才能保證復合材料制品的質(zhì)量和性能,而這些都與增強材料的性質(zhì)、織物結(jié)構(gòu)、定型劑種類和預成型體制造工藝等密切相關(guān)。下面幾方面是纖維預成型體所要求的工藝特性。 (1) 浸滲特征:纖維預成型體最基本的要求是樹脂必須對它能充分浸滲,并且要在盡可能小的壓力下和盡可能短的時間內(nèi)完成這一過程。其中一個重要的浸滲參數(shù)是纖維預成型體的滲透率。滲透率與纖維預成型體的紡織結(jié)構(gòu)有密切關(guān)系,特別是纖維的排列方向、纖維的體積分數(shù)和纖維對樹脂浸潤性等。 (2)纖維的浸潤性:這種性能基于纖維和樹脂的自由表面能,由它們的接觸角決定的。為了使樹脂充分浸潤纖維,纖維的表面能必須大于樹脂的表面能,因此商業(yè)用的纖維大都進行了表面處理,采用定型劑時,必需考慮樹脂對含定型劑纖維的浸潤性,通過定型劑處理能提高浸潤性。 (3) 預成型體的抗沖刷性:對于纖維體積分數(shù)高的預成型體,為了提高浸滲速率,通常需要比較大的樹脂注射壓力,為保證纖維的排列方向不被沖亂,這就要求預成型體有良好的抗沖刷性,采用定型劑預成型時,保證定型劑有一定的粘接力和剛度。 (4)預成型體的均勻性:預成型體的各部分浸滲參數(shù)相差盡可能的小,以利于樹脂能按照預計方向流動。因此制備預成型體時均勻分散定型劑很重要。 (5)預成型體的可操作性:預成型體的可操作性依賴于預成型體的剛性和預成型體的整體性,目的是使預成型體在工藝過程中易于操作而不會對纖維的排列和體積分數(shù)造成影響。 (6)預成型體的表面平整性:對于表面質(zhì)量要求高的制件(如汽車零部件),預成型體的表面質(zhì)量直接影響著產(chǎn)品的使用,有時還必須通過應用膠衣樹脂才能達到使用要求。 短切纖維噴射預成型體制備方法,即經(jīng)常提到的直接纖維預成型,短切纖維與粘結(jié)劑一起被噴射到開有預留孔的模板或網(wǎng)屏上(通常采用組合的粗紗和熱固性樹脂乳膠作為膠黏劑),噴灑完成后需將預成型體烘干,也可以采用粉末和纖維形式的熱塑性膠黏劑。在傳統(tǒng)工藝中,通過有孔模板吸入空氣,在沉積纖維的同時保持或部分干燥預成型體。噴射完后,加熱預成型體至膠黏劑固化定型。其工藝特點是原材料成本低,可以生產(chǎn)凈形預成型體。但由于短切纖維力學性能低,限制了其應用范圍;而且模具工裝費用成本較高,能量消耗大。
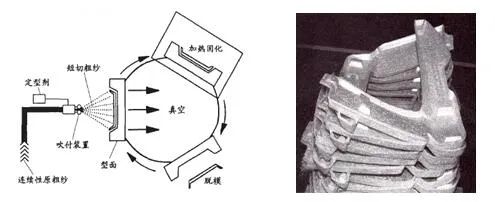
CompForm預成型是唯一能使用多種增強材料的成型工藝,能使用一種或幾種增強材料混合成型。該預成型體工藝使用液態(tài)熱塑性粘結(jié)劑,通過紫外線照射固化。由于這些膠粘劑由紫外線提供固化能,固化非常迅速且可通過幾種方式實現(xiàn)。CompForm工藝的特點就是能制造復雜的預成型體,通過逐次的預成型或組合程序。這種預成型工藝制成的預成型件可包括夾心材料及嵌件。 由于粘結(jié)劑是熱塑性的,可以實現(xiàn)穩(wěn)定的工藝重復,或不止一步地進行預成型。逐次的組合,就像裝配線上的焊接工藝一樣,都能很容易地實現(xiàn)。另一方面,在選定部分可使用不透明的遮光罩,使得選定部分的粘結(jié)劑不固化以備后面的組裝或成型用。被遮住沒有固化的區(qū)域,允許復雜的形狀被“展開”成簡單的形狀,經(jīng)“再包裹” 成最終的形狀,然后將前面的遮光部位用紫外線照射固化膠粘劑進行固化。 P4預成型體工藝項目受ACC(汽車復合材料國際聯(lián)合組織)的Focal Project Ⅱ和Ⅲ的支持。是為了實現(xiàn)Focal Project Ⅱ為目的,即制備復合材料小噸位卡車軸承箱的SRIM模塑要求的高容量纖維預成型產(chǎn)品。 P4包括三種主要的步驟:纖維鋪層、固化及預成型脫模。工藝的第一步是切碎纖維及粘結(jié)劑的附著。纖維粗紗被切碎后與熱塑性粉末狀粘結(jié)劑一起噴射到預成型模具上。通過表面的正向氣流保證切碎纖維固定在模具表面。一旦噴射完成,模具鎖緊,預成型體被壓縮到所要求的厚度。然后向模具內(nèi)吹熱空氣熔化粘結(jié)劑。粘結(jié)劑被熔化后,熱氣流停止,粘結(jié)劑固化使纖維定型。模具開模,完成預成型體脫模。與短切纖維預成型制備工藝比較, P4工藝從本質(zhì)上和原理上并沒有太大的區(qū)別。只在最后定型階段上,P4工藝用到了對模壓制方法,這樣將有效保證纖維的體積含量,同時為預成型體提供足夠的剛度,即能生產(chǎn)高度堅固,凈外形/凈尺寸的預成型體,而這僅需要通過適當?shù)哪>邅韺崿F(xiàn),模具能將預成型體壓縮到要求的厚度,同時也增加了整個預成型體的剛度和可操作性。凈外形/凈尺寸特征可通過真空消除玻璃纖維的過多噴涂,也可通過凈邊模具設(shè)計來滿足分模邊的確定。該凈尺寸能省去修理操作的需要。 預成型工藝的自動控制與直接纖維預成型相比有幾大優(yōu)點:控制噴射程序提供了可重復性與零件的一致性;控制玻璃纖維附著能消除超量噴射,因此減少了玻璃纖維廢料;自動控制配合高級切碎槍預計能提供在快的循環(huán)周期內(nèi)噴射復雜形狀。但P4預成型體工藝的可重復型是建立在完全自動化的機械上膠預成型工藝,整個工藝自動化通過機械手和自動機械控制來完成。
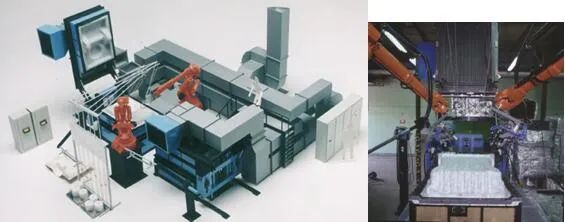
采用含有定型劑的片狀增強材料,鋪貼在模具上,通過加溫、加壓、冷卻和脫模等工序,靠物理作用固定片狀纖維。增強材料主要是織物和玻璃纖維氈。片狀預成型分為熱模壓成型和直接成型。直接成型不需要預成型體;熱模壓成型是通過加熱,熔化定型劑并加壓成型的方法(見圖6-7)。(1)增強材料的裁剪:把增強材料裁剪成比產(chǎn)品外形尺寸大10 cm的形狀;在預成型模具里不加熱條件下模壓;切成所需的形狀。(3)在加熱模具里加熱加壓,溫度和時間與定型劑有關(guān),一般為110~150℃,60~180 秒。 其優(yōu)點為適合形狀單一的產(chǎn)品;周期短;可自動化。缺點為不適合深度大的形狀;表面上易留增強材料的花紋;有10%的損失;易出現(xiàn)富樹脂部位。
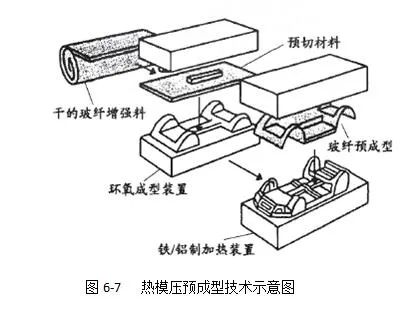
黏度:樹脂黏度范圍在0.1~1Pa?s,一般為0.12~0.5 Pa?s。黏度太高或太低可能導致浸漬不良,或形成大量的孔隙和未被浸漬的區(qū)域,影響制品的性能和質(zhì)量。黏度太高的樹脂需要較高的注射壓力,容易導致纖維被沖刷。 相容性:樹脂對增強材料應具有良好的浸潤性、匹配性和界面性能。 反應活性:RTM工藝用樹脂的反應活性應表現(xiàn)為兩個階段,在充模過程中,反應速度慢,不影響充模,充模結(jié)束后,樹脂在固化溫度條件下開始凝膠,并迅速達到一定的固化程度,這樣才能減少模具占用時間,提高生產(chǎn)效率。 收縮率:樹脂收縮率要低,樹脂收縮率過大會增加孔隙率和制品裂紋的機會。 模量:在滿足力學性能的前提下,樹脂模量適中。高模量的樹脂產(chǎn)生高熱應力,容易引起制品變形和產(chǎn)生裂紋。 韌性和斷裂延伸率:樹脂這兩個指標主要與制品抗沖擊與耐裂紋性能成正比,較高值可提高樹脂耐熱裂紋的能力。 用于RTM的聚酯樹脂用通用型、低收縮性以及其它一些特殊類型 (1)英國Joton Polymer公司生產(chǎn)的Norpol 42-10是一種中等活性、剛性的鄰苯樹脂。該樹脂在23℃的物理性能為:黏度180~210mP?s,密度1.1g/cm3,膠凝時間12~18分鐘。其性能列在表6-2中
性能 | 純樹脂 | 玻纖氈增強 | 性能 | 純樹脂 | 玻纖氈增強 |
纖維含量(重量)% |
| 25~30 | 35~40 | 拉伸強度/MPa | 140 | 155 | 215 |
拉伸強度/MPa | 70 | 110 | 160 | 拉伸模量/GP a | 3.6 | 7.2 | 10 |
拉伸模量/GP a | 3.7 | 8.0 | 10.3 | 沖擊強度/kJ/m2 | 12 |
|
|
斷裂延伸率/% | 3.5 | 2.0 | 2.2 | 熱變型溫度/℃ | 67 |
|
|
Norpol 42-96是一種中等反應性的不飽和聚酯樹脂,特別適用于低壓注射工藝和發(fā)泡注射工藝。Norpol 42-96樹脂的發(fā)泡過程,是先加入1.25%的發(fā)泡劑Luper-Foam329,而后再加入3%的Luperox DP33促進劑。這種聚酯泡沫制品的密度,要比通用聚酯的輕得多。Norpol 42-96的膠凝時間約為9~14分鐘, 含15%玻璃纖維氈復合材料的密度約為0.9~1.0g/cm3,抗拉強度為20~30MPa,抗拉模量為2.7~3.2GPa,抗彎強度為45~55 MPa,擺錘式?jīng)_擊強度為31kJ/m2。當玻璃纖維含量為25%時,其密度約為1.0~1.2g/cm3,抗拉強度為60~70 MPa,抗拉模量為6.3~7.2GPa,抗彎強度為100~110 MPa,擺錘式?jīng)_擊強度為46 kJ/m2。 Norpol 80-1-06阻燃型樹脂,是用于樹脂注射工藝的一種自熄式快速固化的聚酯樹脂。其玻纖增強制品,根據(jù)英國標準BS476Part7測試標準,符合自熄性要求。該樹脂黏度較低,能快速浸濕玻璃纖維增強材料。 (2) 意大利Alusuisse公司的RTM工藝用樹脂Disititron 21182和Disititron 441,可以滿足用戶的不同要求。其性能列于表6-3
表6-3 Disititron樹脂的性能
性能 | DS 21182 | DS 441 | 性能 | DS 21182 | DS 441 |
黏度(25℃)/mP.s | 700 | 450 | 拉伸模量/GPa | 3.8 | 3.6 |
纖維含量(重量)% | 30 | 35 | 斷裂延伸率/% | 2.5 | 3 |
凝膠時間(75℃)/s | 170 | 210 | 彎曲強度/MPa | 100 | 130 |
熱變形溫度/℃ | 95 | 75 | 彎曲模量/GP a | 3.7 | 3.8 |
拉伸強度/MPa | 60 | 70 |
|
|
|
(3)金陵帝斯曼樹脂有限公司生產(chǎn)的RTM樹脂主要有三個牌號,其性能見下表,其中以P6-988KR最為常用。
表6-4 帝斯曼公司生產(chǎn)的RTM樹脂性能
品牌 | 產(chǎn)品牌號 | 類別 | 黏度 | 凝膠時間 | HDT | 拉伸強度 | 斷裂延伸率 | 特性及說明 |
Synolite | 1777-G-4 | 鄰苯 | 185 | 28-31 | 91 | 80 | 4.1 | 用于真空輔助注射成型,優(yōu)良的浸潤性能,適合制造結(jié)構(gòu)復雜制品 |
Synolite | 4082-G-22 | 鄰苯 | 185 | 9-15 | 63 | 70 | 2.0 | 機械性能好,玻纖浸潤優(yōu)良,固化性能好,放熱峰低,中國船級社認證 |
Palatal | P6-988KR | 鄰苯 | 325 | 15-25 | 70 | 70 | 3.5 | 高延伸率、高沖擊強度、流動性好 |
德國BASF公司的Palapreg R30-01V低收縮樹脂,可以達到A級表面質(zhì)量。只要工藝條件合適,該系統(tǒng)可適用于各種RTM用途,不管是否使用膠衣,都能獲得良好的表面質(zhì)量。RTM成型時,模具的最低溫度為60℃,最佳溫度為80℃。當模塑制品在常溫下固化,放置24小時后,制品的收縮率約為0.11%。若制品在80℃下固化,放置24小時后,尺寸則沒有變化。成型的復合材料性能為:彎曲強度175Mpa,彎曲模量7Gpa,拉伸強度120Mpa,沖擊強度80KJ/m2。 美國Ashland Chemical公司生產(chǎn)的Arotran樹脂, 由于采用了新的聚酯化學技術(shù),可用于制造A級汽車覆蓋件。該樹脂的模塑溫度為60℃,聚合反應中出現(xiàn)的物理微孔,可消除收縮,從而得到光滑表面。 其配方和工藝條件為;100份樹脂,70份碳酸鈣和2份Luperso/DDM-9。增強材料包括一層表面氈,24 %的連續(xù)纖維氈及定向布氈,RTM注射機的氣壓為275-550KPa,樹脂與過氧化物的比率為100:1.2。 乙烯基樹脂是用環(huán)氧樹脂和不飽和酸反應制成的,其分子鏈末端具有高交聯(lián)度、高反應活性的雙鏈,化學性能穩(wěn)定,其中穩(wěn)定的苯醚鍵使乙烯基樹脂耐腐蝕。另外,酯基只位于分子鏈端部,固化反應時交聯(lián)也只在端部進行,整個分子鏈都不參加反應。因此,分子鏈可以拉伸,并表現(xiàn)出比較好的韌性,延伸率可以達到4%~8%。由于乙烯基酯獨特的分子鏈和合成方法,使其固化物的力學性能接近環(huán)氧,工藝性能類似聚酯。具有高度耐腐蝕性。它的耐酸性能優(yōu)于胺類環(huán)氧,耐堿性優(yōu)于酸類固化環(huán)氧和不飽和聚酯。乙烯基酯分子中的羥基,增加了樹脂對玻纖的浸潤性。Dow化學工業(yè)公司生產(chǎn)的Derakane牌號的乙烯基酯樹脂可用于RTM工藝。
樹脂體系 | 說明 | 黏度/Mp.s | Tg/℃ | HDT/℃ | 斷裂延伸率/% |
Derakane411C-50 | 雙酚A乙烯基酯樹脂 | 125 | 240 | 215 | 5~7 |
Derakane 530 | 溴代雙酚A環(huán)氧乙烯基酯樹脂 | 450 | 270 | 230 | 4~5 |
Derakane510A-40 | 溴代雙酚A環(huán)氧乙烯基酯樹脂 | 250 | 260 | 230 | 4~5 |
Derakane 470-36 | 酚醛型環(huán)氧乙烯基酯樹脂 | 200 | 305 | 300 | 3~4 |
Derakane 8084 | 韌性雙酚A環(huán)氧乙烯基酯樹脂 | 375 | 230 | 180 | 8~10 |
XU71835.OIL | 高韌性交聯(lián)乙烯基酯樹脂 | 350 | 250 | 200 | 6~8 |
國內(nèi)乙烯基樹脂比較有代表性的生產(chǎn)企業(yè)是上海華東理工大學華昌聚合物有限公司 ,該公司生產(chǎn)MFE系列的乙烯基酯樹脂。
表6-6 MFE-RTM-200樹脂澆鑄體力學性能
檢驗項目 | 檢驗結(jié)果 | 測試方法 | 檢驗項目 | 檢驗結(jié)果 | 測試方法 |
拉伸強度MPa | 63.94 | GB/T 2568 | 彎曲模量GPa | 3.39 | GB/T 2570 |
拉伸模量GPa | 2.75 | GB/T 2568 | 壓縮強度MPa | 108.68 | GB 2569 |
延伸率% | 4.22 | GB/T 2568 | 沖擊強度KJ/m2 | 12.42 | GB 4493 |
彎曲強度MPa | 126.38 | GB/T 2570 | 熱變形溫度℃ | 105 | GB 1634 |
環(huán)氧樹脂主要用于成型高性能復合材料,一個環(huán)氧樹脂體系是否能適用于RTM成型,是否能成為高性能復合材料的樹脂基體,不僅與環(huán)氧樹脂品種有關(guān),同時亦取決與所用固化劑及促進劑。為使樹脂體系適用于RTM成型,固化劑體系在室溫下應為低黏度液體,與環(huán)氧樹脂配合后樹脂在注射溫度下具有良好的儲存穩(wěn)定性,固化樹脂具有良好的耐熱性、高強度、高韌性。目前常用的固化劑為液體胺類和多官能團的液體酸酐等。 針對高性能環(huán)氧樹脂體系工藝性差的問題,另一個解決的方法是通過升溫或加入稀釋劑。但升高溫度將縮短工作期,而活性稀釋劑在有效降低體系黏度的同時又常常降低制品的耐熱性。所以,開發(fā)研制耐高溫活性稀釋劑也是環(huán)氧樹脂體系改性的一條重要途徑。 適用于高溫成型工藝的代表性環(huán)氧樹脂主要有Ciba-Geigy公司開發(fā)的LSU940/XU205和3M公司開發(fā)的PR 500環(huán)氧樹脂體系,主要應用與航空復合材料制件。室溫成型用環(huán)氧樹脂通常是雙組分的,由環(huán)氧樹脂和室溫下黏度較小的固化劑組成。代表性的有CYTEC公司的CYCOM 823和HEXCEL公司的RTM6。國內(nèi)比較有代表性的室溫注射RTM樹脂有北京航空材料研究院研制的3266環(huán)氧樹脂體系。3266是一種80℃固化120℃后處理、中溫75℃長期使用的結(jié)構(gòu)性RTM專用環(huán)氧樹脂,主要應用在高動態(tài)載荷的部件如飛機螺旋槳槳葉、艦船或魚雷推進螺旋槳槳葉以及其他主承力結(jié)構(gòu)上。 表6-7 幾種室溫成型環(huán)氧樹脂澆鑄體性能比較
測試項目 | 3266 | CYCOM 823 | RTM 6 |
密度(g/cm3) | 1.2 | 1.23 | 1.14 |
拉伸強度/MPa | 80.58 | 80 | 75 |
拉伸斷裂應變/% | 6.5 | / | 3.4 |
拉伸模量/GPa | 3.47 | 2.9 | 2.8 |
彎曲強度/MPa | 151.4 | 144 | 132 |
彎曲模量/GPa | 3.77 | 3.4 | 3.3 |
干態(tài)Tg/℃ | 120(DSC) | 125 |
|
雙馬來酰亞胺樹脂力學性能好,高溫穩(wěn)定性突出,低毒、低煙。主要缺點是黏度高、韌性差。用于RTM工藝需要改性,主要采用自由基共聚、Michael加成、Diels-Alder反應等手段獲得。國外代表性樹脂有Ciba-Geigy公司開發(fā)的Matrimid 5292,Technochemie公司生產(chǎn)的Compimide 65 FWR,DSM公司開發(fā)的Desbimid RTM樹脂。 國內(nèi)典型的雙馬來酰亞胺樹脂有中國航空第一集團復合材料特種結(jié)構(gòu)研究所用于RTM工藝雷達天線罩的F.JN-5-02,北京航空工藝研究所開發(fā)的QY8911-Ⅳ等。 該類樹脂主要用于航空航天領(lǐng)域用的耐高溫復合材料結(jié)構(gòu)部件。 RTM工藝過程包括樹脂充模流動、熱傳遞和固化反應。其中熱傳遞和固化反應是其它復合材料工藝所共有的,工藝控制重點是充模流動問題。 在RTM充模過程中,模具型腔內(nèi)填充著纖維預成型坯,可以稱之為纖維床,其中包含固體相——纖維和流動相——空氣。樹脂的充模過程就是保證樹脂流過這些不規(guī)則的孔隙并將空氣置換出去,使樹脂充滿孔隙的過程。樹脂在這些不規(guī)則的孔隙中流動是非常復雜的,同時存在兩種類型的流動,一種是纖維束間的宏觀流動,另一種是纖維束內(nèi)的微觀流動。這兩種流動在充模過程中相互競爭,可能導致浸潤不良或氣泡的包裹。 當注射壓力較低時,纖維束內(nèi)的毛細作用力起主要作用,流體的流動前沿形態(tài)如圖6-8(a)所示,纖維束內(nèi)的流動前沿領(lǐng)先于纖維束間的流動前沿,當領(lǐng)先的流體前沿沿橫向流動匯合時,纖維束內(nèi)未被排出的空氣即被包裹,形成纖維束間的大氣泡;反之,當注射壓力較高時,毛細壓力同動力壓力相比作用較小,因而纖維束內(nèi)流體的流動前沿落后于纖維束間的流動前沿,如圖6-8(b)所示。當流動前沿橫向流動匯合時,形成纖維束內(nèi)部的小氣泡。氣泡含量是復合材料質(zhì)量的重要指標之一。氣泡的存在使纖維浸潤程度低、粘結(jié)性差,使復合材料部件的機械強度不一致及表面質(zhì)量低劣;同時易引起應力集中,引發(fā)裂紋的產(chǎn)生,降低了復合材料的耐久性、抗疲勞性及耐候性等。
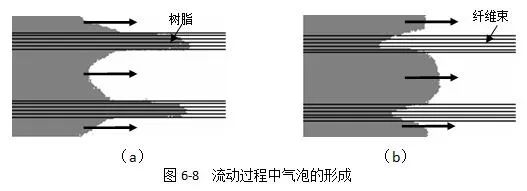
氣泡形成制品的微觀缺陷,主要存在于纖維束間或纖維束內(nèi)單絲間,而干斑的產(chǎn)生則是制品的宏觀缺陷。處理纖維預成型體時,經(jīng)常出現(xiàn)預成型體彎曲、織物邊緣松散、局部預成型體滲透性能變化等問題。在裁剪預成型體時,一般很難達到精確的尺寸精度,纖維束的松散性會使邊緣處的纖維體積含量減小。此外,當模具設(shè)計不合理或合模不當時都容易使預成型體和模腔壁間及拐角處產(chǎn)生縫隙,而這一縫隙則形成了樹脂的優(yōu)先流道,樹脂在這種通道中的流動超前于在預成型體中的流動,破壞了正常的流動前沿模式,這種效應稱為“邊緣效應”或“流道效應”。這類由于預成型體受剪切、壓縮或者壓緊效應,尤其是邊緣效應引起的增強材料性能變化對充模過程有重要的影響,易引起纖維浸漬不充分、干斑等問題。一般的流道效應區(qū)為毫米級,在有些情況下,1~2mm的競流區(qū)對充模過程也會有相當大的影響,使制品產(chǎn)生大面積的干斑。 對RTM工藝充模過程的分析研究都是建立在流體流經(jīng)多孔介質(zhì)的理論基礎(chǔ)上,采用達西定律為動量控制方法。達西定律由Henry Darcy 于二十世紀中期根據(jù)一系列是實驗結(jié)果提出的,在土壤學中有著廣泛應用。達西定律中描述,流體流經(jīng)多孔介質(zhì)的速度與所施加的壓力梯度成正比,而與流體的黏度成反比。達西定律是動量平衡方程的特殊形式,可以直接代入連續(xù)方程,而得到關(guān)于壓力的控制方程。 對于水平流動,不計重力的情況下,達西定律可表達如下:
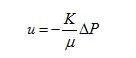
其中,u(m/s)為流體的速度矢量,K(m2)為預成型體的滲透率張量,為預成型體的內(nèi)在屬性,μ (Pa?s)為流體的黏度,以及 P (Pa/m)為壓力梯度??梢钥闯觯_西定律是一種體積上的平均描述,流體和纖維預成型體之間所有的復雜的相互作用都依靠滲透率張量來體現(xiàn), 滲透率是描述充模過程中流體的流動特性的關(guān)鍵參數(shù),獲得準確的滲透率數(shù)據(jù)對于獲得和實際生產(chǎn)相一致的模擬結(jié)果起著重要的作用。對于各向異性多孔介質(zhì),滲透率張量可表達如下:
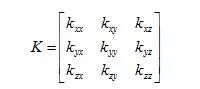
對于特別的正交各向同性預成型體,當局部坐標與纖維預成型體的主方向一致時,其滲透率張量可描述為:
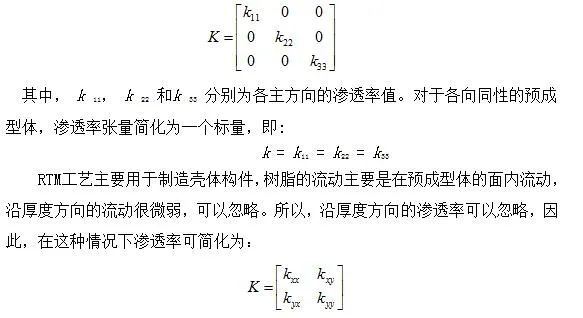
RTM 應用中纖維預成型體滲透率通常由三個途徑獲?。簩嶒灉y量,解析求解和數(shù)值估計。
RTM工藝的流動模擬可以定性的預測樹脂流動過程。如果輸入的參數(shù)合理可靠,注射壓力、流動速率、流動狀態(tài)等可以通過模擬準確預報。建立分析技術(shù)的核心問題是如何獲得輸入的重要參數(shù)數(shù)據(jù),如滲透率、樹脂化學流變特性、熱擴散以及邊緣流動等。這些參數(shù)與復合材料的樹脂體系、增強材料體系、模具以及工藝等都有緊密的聯(lián)系。 液體流動過程有限元模擬理論是當今模擬技術(shù)的難點和熱點,目前關(guān)于樹脂流動的有限元模擬軟件已趨于成熟,如荷蘭Polyworx公司開發(fā)的RTM-Worx、法國ESI公司開發(fā)的PAM-RTM和美國MoldFlow公司開發(fā)的MOLDFLOW等。應用這些流動模擬系統(tǒng),參照實際產(chǎn)品的使用要求、性能要求和成型工藝等參數(shù),建立實際產(chǎn)品有限元模型,可以有效模擬產(chǎn)品的生產(chǎn)過程,指導實際產(chǎn)品的生產(chǎn)。 通過流動模擬技術(shù)在實際產(chǎn)品生產(chǎn)過程中應用的研究,可以得出流動模擬技術(shù)工程化應用的一般性流程:(1)對制件進行計算機幾何建模,并借助有限元方法對模型進行有限元剖分;(2)根據(jù)制件的幾何形狀選擇若干種可行的樹脂注射方式;(3)選擇和測定樹脂流動模擬所需的各個參數(shù),包括注射壓力、預成型體的滲透率和纖維體積含量,以及樹脂黏度等;(5)綜合考慮樹脂流動時間和最后填充位置,以及工藝操作的難易程度等各種因素,選擇最優(yōu)的樹脂注射方式,指導實際生產(chǎn)。下面是運用RTM-Worx軟件對天線罩RTM工藝充模過程進行模擬的例子。制件的幾何形狀及尺寸如圖6-9所示。
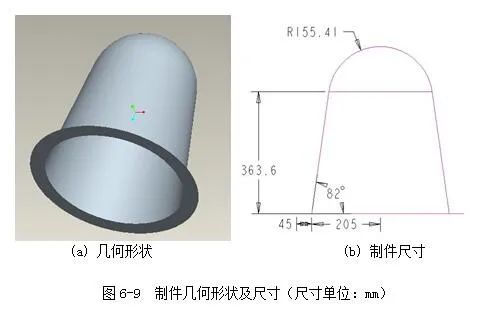
模擬時注射壓力設(shè)為0.5MPa,假定增強材料預成型體各向同性、滲透率為1×10-10m2且分布均勻,纖維體積含量為40%,球冠和工作區(qū)的厚度設(shè)為14mm,圓環(huán)處的厚度設(shè)為20mm,樹脂黏度設(shè)為0.4 Pa?s,模擬結(jié)果如圖6-10所示。
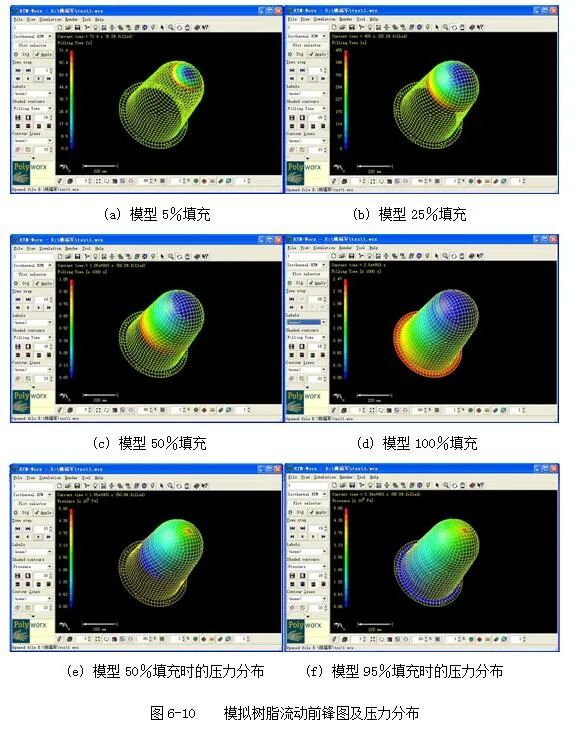
樹脂注射設(shè)備包括加熱恒溫系統(tǒng)、混合攪拌器、計量泵以及各種自動化儀表。注射機按混合方式可分為單組分式、雙組分加壓式、雙組分泵式、加催化劑泵式4種?,F(xiàn)在用于批量生產(chǎn)的注射機主要是加催化劑泵式。 瑞典的Aplicator公司制造的RI-2設(shè)備,使RTM工藝朝高質(zhì)量、高速度的全系統(tǒng)生產(chǎn)方面邁了一大步。它既可以用于制造高玻璃纖維含量的結(jié)構(gòu)件,也可以生產(chǎn)A級表面的汽車部件。RI-2有1個單沖程液壓泵,2個輸送氣缸,1個用于輸送樹脂,1個用于輸送催化劑。有1個專用的輸入閥直接將泵和模具連接起來,混合料就由該閥流進,沒有溶劑和樹脂暴露于工作區(qū)。該系統(tǒng)及噴槍都由1臺程控機PLC)控制。所有的注射參數(shù)都可預先設(shè)定,供生產(chǎn)選擇。注射在一個連續(xù)的沖程內(nèi)進行,這可避免傳統(tǒng)活塞泵中因壓力下降以及流量脈動所引起的問題。控制注射既可以用壓力,也可以用流量。通過一個在噴槍或模具內(nèi)的壓力傳感器,可以在注射過程中以設(shè)定的壓力注射。
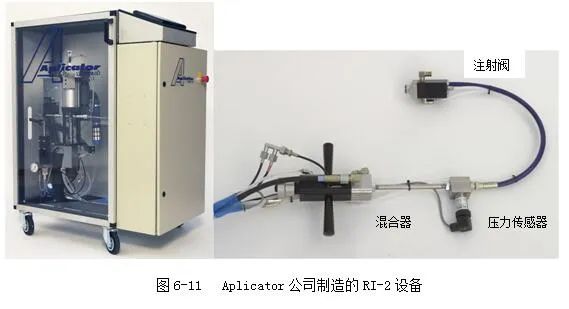
美國液控系統(tǒng)公司(LIQUID CONTROL SYSTEMS)制造的Multiflow RTM設(shè)備,可對從幾克到數(shù)百公斤的反應樹脂體系進行計量,混合并注射進低壓力閉合模。這種機器的特點是有一臺Posiload正向轉(zhuǎn)換活塞泵,它使黏度的測量精確達±0.1~0.5%,且在溫度、壓力或材料黏度變化時不受影響。這種泵沒有大多數(shù)泵采用的輸入檢驗閥,通過真空輔助,可確保計量管完全充滿料。 Multiflow CMFH型用于制造大型增強材料部件,輸入量為45KG/min。可適用于多種樹脂體系,包括聚酯、環(huán)氧,聚氨酯和甲基丙烯酸樹脂。它可以注射未稀釋的MEKP和BPO乳劑。使物料中催化劑濃度達0.5%。泵壓力比從1:1到200:1。該機可處理的填料很多,包括碳酸鈣、氫氧化鋁以及空心玻璃微珠,計量精確度不受閉模引起的反向壓力的影響。
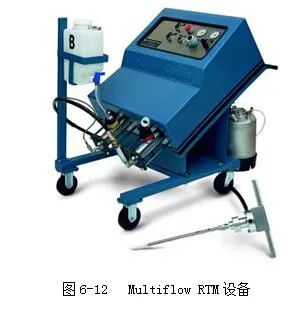
美國Glas-Craft公司生產(chǎn)的LPI型注射機,在國內(nèi)引進較早,是一種相對簡單的注射設(shè)備。該系統(tǒng)的特色為在18913—00型11:1的物料泵上安裝了SP-85催化劑伺服泵。催化劑和樹脂以容積計量,通過LI噴槍進行混合和分配。 18913-00型是一種雙球往復式泵,即使在低操作壓力下,它也有輸出能力,來滿足物料的需求量。它采用一個13cm直徑的氣缸,行程為10cm,能達到的最高傳遞速率為9.5L/min。SP-85催化劑泵是一個不銹鋼正向置換泵,可在0.5~4.5%范圍內(nèi)準確分配催化劑。它有一個緊固的聯(lián)動機械,可以很容易地調(diào)節(jié)微量的催化劑百分量。LI內(nèi)混合噴槍的特色在于有一個新穎的混合頭和18cm長的靜態(tài)混合管。它們組合在一起可以使樹脂和催化劑在低壓下得到很好的混合,保證制品均勻、連貫的固化。這套系統(tǒng)還有一個催化劑流量監(jiān)測器,如果分配時流體壓力偏離正常設(shè)定值,報警器響,系統(tǒng)被切斷。
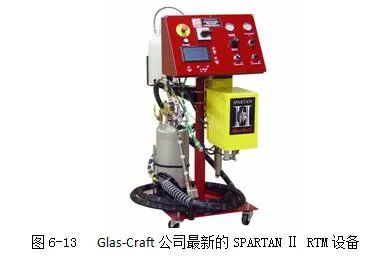
英國P1astech TT公司生產(chǎn)的注射機考慮到了多種生產(chǎn)參數(shù)的集中控制問題,是一種很有特色的低壓連續(xù)注射樹脂設(shè)備,其中Megaject Pro型是自動化程度最高的一種(見圖6-14),主要特點為: (1)系統(tǒng)的工作控制全部通過一個液晶觸屏面板來完成,屏幕界面分為管理員界面和用戶界面,并采用密碼保護。可以為多個模具設(shè)定注射工藝參數(shù):注射量,注射壓力,引發(fā)劑用量、加熱器溫度等,并實現(xiàn)注射全過程的一鍵控制。 (2)注射槍頭位置設(shè)置樹脂壓力傳感器(MPG),通過MPG可以根據(jù)設(shè)定的壓力控制注射速度,防止產(chǎn)生比實際工藝要求高得多的壓力。 (3)引發(fā)劑泵的調(diào)節(jié)采用電機控制,可以根據(jù)設(shè)定參數(shù)在工作過程中變化,保證了樹脂在模內(nèi)引發(fā)同步。引發(fā)劑流量檢測裝置會以曲線的形式給出實際流量,當偏離設(shè)定值時,就會報警。 (4)自動凝膠系統(tǒng)在注射結(jié)束后開始計時,在過了安全期后,報警器就會發(fā)出警報。繼續(xù)注射,報警器復位但不取消,要取消它,需啟動自動清洗鍵,用溶劑清洗混合器。 (5)特殊的噴槍空氣清洗控制器,它可以減少清洗劑的用量,減少污染,使其再被利用,同時空氣清洗也使混合器得到干燥,避免了混合器受污染。 (6)Megaject配裝一個氣動真空器,使用者可以方便地控制操作,為模具提供真空。
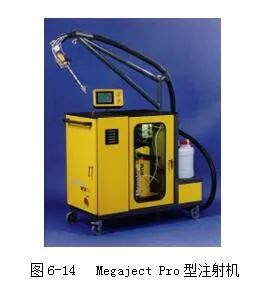
RTM是在低壓下成型,模具剛度相對要求低,可以使用多種材料來制造模具。常用的模具類型有玻璃鋼模具,電鑄鎳模具、鋁模具、鑄鐵模具和鋼模。表6-8列出了各種類型模具的比較。
表6-8 不同類型的模具比較
| 玻璃鋼模 | 電鑄鎳模 | 鋁模 | 鑄鐵模 | 鋼模 |
強度/MPa | 150~400 | 300 | 50~500 | 100~200 | >300 |
模量/GPa | 7~20 | 200 | 71 | ~150 | 210 |
韌性 | 沖擊引起損傷 | 耐低沖擊 | 易造成劃痕 | 不易損傷 | 不易損傷 |
密度g/cm3 | 1.5~2 | 8.9 | 2.7 | 7.2 | 7.8 |
熱膨脹系數(shù)×10-6℃ | 15~20 | 13 | 23 | 11 | 15 |
熱導率/W·m-1·K-1 | ~1 | ~50 | 200 | 70 | 60 |
比熱容/ J·kg-1·℃-1 | ~1000 | 460 | 913 | 500 | 420 |
最高使用溫度/℃ | 80 | >樹脂固化溫度 | >樹脂固化溫度 | >樹脂固化溫度 | >樹脂固化溫度 |
公差 | 固化收縮變形 | 取決于原模 | 精度高 | 精度高 | 精度高 |
表面光潔度 | 可拋光 | 拋光改善光潔度 | 拋光改善光潔度 | 不如鋁和鋼模 | 拋光改善光潔度 |
修復 | 膠衣?lián)p壞容易修復,增強層損壞難修復 | 不易修復 | 容易 | 容易 | 容易 |
制造周期 | 2~4周 | 30~40天 | 30~40天 | 30~40天 | 30~50天 |
RTM模具的結(jié)構(gòu)設(shè)計包括產(chǎn)品結(jié)構(gòu)分型;嵌模、組合模、預埋結(jié)構(gòu)、夾芯結(jié)構(gòu)等模具結(jié)構(gòu)形式;專用鎖緊機構(gòu)、脫模機構(gòu)、專用密封結(jié)構(gòu);真空結(jié)構(gòu)形式;模具層合結(jié)構(gòu)、剛度結(jié)構(gòu)形式、模具加熱形式等。模具結(jié)構(gòu)設(shè)計主要遵循以下原則:(1)盡量簡化脫模部件:在制造模具時應考慮產(chǎn)品脫模,覆蓋件兩邊緣要留有一定的脫模角度,各部分的連接處平滑過渡。(3)便于氣體排除:為了有利于氣體的排出,分型面盡可能與樹脂流動的末端重合。(4)模具密封和真空輔助成型:模具采用雙密封結(jié)構(gòu)并且利用真空在浸漬前對模腔抽真空,這樣有利于降低模具變形、降低孔隙率、提高生產(chǎn)效率、減少修整工序。(5)便于活塊的安放:當分型面開啟后,要有一定的空間便于活塊的安放,并保證活塊安放穩(wěn)固,覆蓋件模具的活塊采用真空吸附,利于定位和穩(wěn)固。(6)模具制造的難易性:模具總體結(jié)構(gòu)簡化,盡量減少分型面的數(shù)目,采用平直分型面。
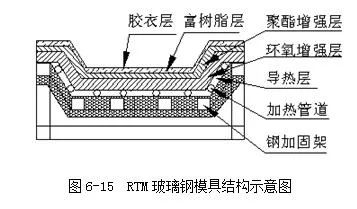
(1)中心位置:注射口選擇在產(chǎn)品的幾何形心,保證樹脂在模腔中的流動距離最短。 (2)邊緣位置:注射口設(shè)計在模具的一端,同時在模具上設(shè)有分配流道,樹脂從邊緣流道注射,排氣口對稱地設(shè)計在模具另一端。 (3)外圍周邊:樹脂通過外圍周邊分配流道注射,排氣口選擇在中心或中心附近的位置。雖然外圍周邊注射的流道也在邊緣,但它是閉合的,排氣口在模具的中心處。 無論怎樣選擇注射口的位置,目的都是保證樹脂能夠流動均勻,浸透纖維。在模具上設(shè)有多個注射口可以提高注射效率,但是要保證不同注射口在流動邊緣到達下一注射口時,該注射口能夠及時開啟,上一注射口及時關(guān)閉,避免出現(xiàn)斷流或紊流造成的流動死角。 排氣口通常設(shè)計在模具的最高點和充模流動的末端,以利于空氣的排出和纖維的充份浸潤。借助流動流動模擬軟件可以比較好地確定理想的注口和排氣口。 模具的密封通常采用不同結(jié)構(gòu)形式的密封條來實現(xiàn),所用到的密封條結(jié)構(gòu)有O型、矩形和異型密封條,材質(zhì)使用硅橡膠比較好。為了保證模具的有效密封和模腔內(nèi)抽真空的需要,經(jīng)常會用到雙密封結(jié)構(gòu)。 在RTM工藝中對模內(nèi)樹脂的加熱方法有兩大類:一是直接加熱法。如美國RP/CMachinery 公司將射頻電能直接通到型腔內(nèi)的樹脂中使樹脂固化,該方法較先進,熱效率最高,但難度大,目前還不成熟;二是間接加熱法:熱能由介質(zhì)(氣、水、油、蒸汽)攜帶,經(jīng)模具背襯、型殼、型面?zhèn)鲗У綐渲?,使樹脂固化。間接加熱法分為三種。 (1)背襯管路法。模具背襯里鋪設(shè)熱介質(zhì)的管路(循環(huán)管路),由于管路離型面有一定距離,而復合材料屬熱的不良導體,熱傳導較困難,因此加熱速度慢,加熱循環(huán)較長。應用此方法要求改善模具材料的導熱性,且選擇較平坦的產(chǎn)品類型,以便鋪設(shè)管路方便易施。 (2) 型殼管路(或電熱絲布)法。型殼里貼近型面鋪設(shè)熱介質(zhì)循環(huán)管路 (或電熱絲布)、熱介質(zhì)流的控制與壓機、模具周邊夾緊的操作相協(xié)調(diào)。1個供熱系統(tǒng)可同時供多個模具,加熱、冷卻的速度最快,但每個模具的成本最高。 (3) 整模加熱法,物料充模后,將整個模具置于固化爐(或高壓釜)內(nèi)加熱,熱能經(jīng)過模具傳導到型腔內(nèi)的樹脂,致使樹脂固化,要求模具材料的導熱性好,固化爐內(nèi)能容納整個模具,如果固化爐尺寸較大,可同時加熱多個模具,本法加熱效率低、固化周期長。 另外美國Sterling Heights公司研制高速RTM工藝,采用鋼模具、模內(nèi)有管路、管內(nèi)通140℃左右的蒸汽,45秒樹脂固化、再配以其他“高速技術(shù)”,如預混合、預催化、特殊單一樹脂、快速投料、快速注射等,模塑周期約1分鐘。
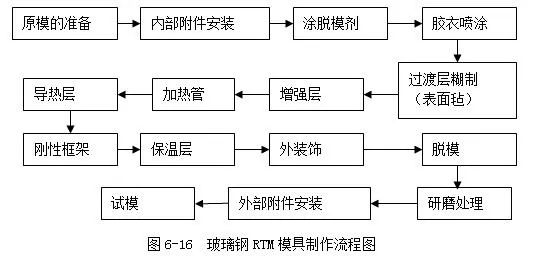
原模的準備工作中最重要的一項是檢驗工作。復合材料的成型是不可逆的,所以每做一工序都需要檢驗驗證其正確合格方可進行下一道工序的施工,這也是保證模具制作出現(xiàn)問題時及時調(diào)整,把損失降到最低的最有效的方法。 內(nèi)部附件包括注入口嵌件,排氣口嵌件,密封條,輔助模內(nèi)頂出件,模內(nèi)導向定位件以及產(chǎn)品預埋件定位機構(gòu)等等。 膠衣層是保證模具表面的基礎(chǔ),厚度宜在0.5~1.0mm,可分2~3次噴涂,固化時間以手觸判斷,觸覺粘而指尖未帶有膠衣為宜。過渡層可用30-50g/m2表面氈糊制,糊制過程中保證不能有氣泡存在,固化后開始糊制增強層,糊制過程中最主要控制鋪層的均勻程度及含膠量均勻程度。 對于形狀簡單、面積較大平板類型的模具,可以在增強層采用氈布交替的鋪層設(shè)計方式,此方法可以進一步提高板殼強度,而曲面較多,形狀復雜的模具直接由短切氈鋪層糊制即可。但根據(jù)不同的模具質(zhì)量要求慎重選擇布類增強,因其強度和含量存在方向性,容易導致模具出現(xiàn)因收縮不均而引起的翅曲變形。 另外,根據(jù)不同的樹脂體系和不同的模具要求及糊制制度進行操作,一般情況下,每固化一次糊制的層數(shù)越少,模具尺寸精確度較高,模具強度低,模具變形機率較?。幌喾疵抗袒淮魏频膶訑?shù)越多,整體強度較大,收縮變形機率也較大。 有加熱層設(shè)計的模具,增強層的制作厚度應為6~8mm,既保證表面強度,其隔熱作作也不至過于突出。加熱層由加熱管路和導熱介質(zhì)構(gòu)成,加熱管路采用銅管制成,并貼附于增強層的表面,先局部固定后,再用導熱材料澆鑄成型。 模具的加固要使用金屬等剛性材料,按板殼理論設(shè)計結(jié)果確定平板單元區(qū)域大小并進行網(wǎng)格式加固,框架焊接完成后必須進行去應力處理,糊在模具背后使其與模具粘接成為一體。有加熱層的模具還要在最后制作保溫層,根據(jù)保溫材料的不同,保溫層厚度一般為50~100mm,澆鑄成型。第七節(jié) RTM產(chǎn)品的典型應用 隨著材料技術(shù)和工藝技術(shù)的不斷發(fā)展,RTM工藝制品已經(jīng)在航空航天、交通運輸、體育用品、船舶、建筑等領(lǐng)域得到了廣泛的應用。由于RTM工藝的特點,在大型部件和高結(jié)構(gòu)性能要求的部件制造方面其工藝優(yōu)勢更為突出。表6-9 RTM在各領(lǐng)域的產(chǎn)品應用
應用領(lǐng)域 | 典型部件 |
航空、航天、軍事 | 通道殼體、門;控制面板;防凍管道部件;驅(qū)動軸;電器盒;發(fā)動機罩上的支撐;風扇葉片;機翼;燃料貯罐;直升機驅(qū)動軸;型桿;紅外線跟蹤裝置底座;發(fā)射管;軍事裝備盒;導彈體;碳/碳部件制造體母模;螺旋槳;天線罩;轉(zhuǎn)輪葉片;盔甲片;靜葉片;太空站支柱;軍用品配件;換向器部件;魚雷殼體以及水下武器原型等 |
汽車 | 車體外殼;保險杠;貨箱頂蓬;變速器;底盤交叉部件;前后底盤零件;板簧;載貨車廂;平底缸式底盤;空間框架等 |
建筑 | 柱子、標桿、商業(yè)建筑的門、框架、施工現(xiàn)場的腳手架、公用電話亭、人孔蓋子、標志牌 |
電器 | 辦公設(shè)備底座、傳真機底座、計算機工作臺面、拋物線型盤碟、天線罩 |
工業(yè) | 冷卻扇葉片、壓縮器機殼、防腐蝕設(shè)備、驅(qū)動軸、電力除塵器、地板、飛輪及飛輪系統(tǒng)部件、減速器、檢驗孔、混合用葉片、防護帽、RTM機器底座、日光反射器、模具欄桿、閥門管 |
船舶 | 船體、小船艙以及零部件、甲板、碼頭支撐柱、緊急避險裝備及底座、螺旋槳、雷達橋、船桅 |
體育運動器材 | 游樂車、自行車架、把手、高爾夫車、高爾夫球棍、雪橇板、帆板、溜冰板、地板、游泳池 |
在該領(lǐng)域的應用主要大型結(jié)構(gòu)部件的整體成型方面,應用實例見表6-10和6-11。
表6-10 (國外)RTM成型技術(shù)在航空航天領(lǐng)域的應用
部件名稱 | 應用領(lǐng)域 | 廠商 | 技術(shù)特點 |
雷達罩 | RAF“狂風”超音速變后掠翼戰(zhàn)斗機 |
| 以編織或機織纖維為增強材料,其纖維質(zhì)量含量達60% |
飛機和氣墊船螺旋槳 | Fokker F50、Saab S340、Bell LCAC 氣墊船、Gruman追蹤者、Piper Cheyenne IV | Dowty航空公司 | 輕質(zhì)、低成本 |
正弦波桿、發(fā)動機入口的密封管、機身框架 | F-22、F117-A戰(zhàn)斗機 | 美國Dow-UT公司 | LCM構(gòu)件的結(jié)構(gòu)性能可與預浸料構(gòu)件相當或更高,且孔隙率更低,每架飛機的成本節(jié)省25,000美元以上 |
隔倉門 | 波音客機 | BP公司 | 采用金屬對模成型,由6件碳纖維/環(huán)氧樹脂的組合構(gòu)件取代了40片鋁材組合構(gòu)件。 |
進氣道、風扇出口護罩、推力反向器和葉柵等 | 飛機 | Dow-UT公司 | 復合材料結(jié)構(gòu)件取代了昂貴的鈦金屬構(gòu)件成功地應用于發(fā)動機和機艙構(gòu)件,已取得聯(lián)邦航空局的認證。 |
方向舵、整體機艙、螺旋槳葉片等 | Bell/SumSung直升機 |
|
|
機翼 | 飛機 | 波音公司 | 該工藝已廣泛應用于制作大型、復雜型面、帶加強筋條乃至帶加強墻和梁的結(jié)構(gòu)件。 |
表6-11 RTM成型技術(shù)在艦船和裝甲車輛上的應用
部件名稱 | 應用領(lǐng)域 | 廠商 | 技術(shù)特點 |
船用防護板 | 艦船 | Hardcore FRP公司 | 具有足夠的強度和剛度,完全可以承受住3000t排量船只的撞擊,但它比同樣大小的鋼制板減重近2700kg |
上層結(jié)構(gòu)板(長20m、面積100m2) | 軍艦 |
| 產(chǎn)品重2噸,利用兩塊10m×50m的真空工作臺面,鋪放35層800g/m2玻纖粗紗,20分鐘注入740kg含預促進劑、熱變形溫度高的乙烯基樹脂,35分鐘凝膠。玻纖含量72%,孔隙含量<1%,樹脂利用率高達95%。此外,在成型工藝過程中在軍艦殼體層壓板里嵌入銅絲網(wǎng)層,能夠?qū)崿F(xiàn)電磁屏蔽功能 |
框架 | Manta Test Vehicle(MTV) | 美國海軍NUWC紐波特分部 | 框架由乙烯基酯樹脂SCRIMP工藝增強E玻纖制成(具有海上偵察、水下搜索和測量、輔助通訊/導航及潛艇跟蹤四種能力) |
船舶結(jié)構(gòu)件 | 船舶 | Hinckley公司 | RFI工藝對樹脂基體的工藝性要求較為苛刻,樹脂在室溫環(huán)境中應具有很好的成膜性,所成薄膜(厚度通常為500μm-1mm)能任意彎曲而不脆裂 |
船舶結(jié)構(gòu)件 | 英國的Sandown級掃雷艇,瑞典的“Visby”隱身輕巡洋艦和“Skjold”隱身巡邏快艇,美國DD21“Zumwalt”級隱身驅(qū)逐艦 |
| 與傳統(tǒng)復合材料成型工藝相比,LCM工藝在成型大厚度、大尺寸制品時具有突出優(yōu)勢,例如:一塊19.5m長、3m寬的潛艇壁板在45min之內(nèi)就可以成型完畢。 |
ACAVP車體 | 歐洲第一輛全復合材料車體裝甲戰(zhàn)車——ACAVP(Advanced Composites Armored Vehicle Platform)戰(zhàn)車 | 英國 | ACAVP車體全部由E-玻纖復合材料與陶瓷材料經(jīng)柔性袋RTM(Soft-Sided Resin Transfer Moulding)工藝整體模塑而成,與普通的裝甲車輛相比,ACAVP重量更輕且防護水平更高。戰(zhàn)車整體減重達25%,同時又能防止雷達信號和熱信號探測,還具有降噪、隔熱、阻燃、防碎片等性能,實現(xiàn)了較好的防護能力和機動性能的統(tǒng)一。 |
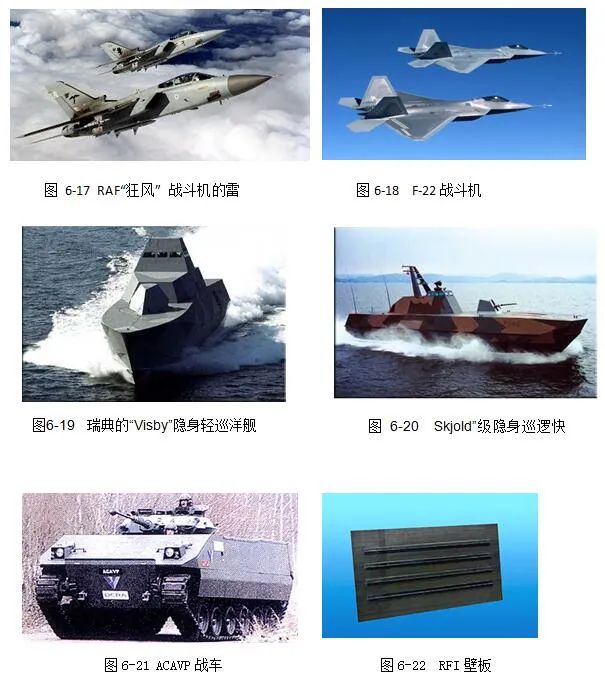
國內(nèi)應用和研究RTM工藝的單位較多,如航空材料研究院、637所、703所、北京玻璃鋼研究設(shè)計院、北京航空航天大學等。應用的產(chǎn)品有雷達罩、全碳纖維復合材料槳葉、導彈穩(wěn)定翼等。 復合材料在汽車工業(yè)中的應用已經(jīng)有相當長的歷史,20世紀90年代以后,汽車工業(yè)開始使用RTM工藝制造零部件。汽車工業(yè)是RTM應用最早、規(guī)模最大的領(lǐng)域。 1970年前后,用RTM工藝加工Corvette車型的儀表盤,GM試驗研究的全復合材料承力構(gòu)架,達到鋼制構(gòu)架性能而減重20%。近年來采用RTM工藝已工業(yè)化生產(chǎn)了FIEERO轎車和雪佛萊LUMINA“子彈頭” 汽車等車型的車身覆蓋件和零部件,年產(chǎn)量已分別達到6.5~10萬輛。1992年Chrysler研發(fā)出Viper跑車的RTM車殼;1994年Fort研發(fā)出RTM Transit商用車的高頂,1995年研制RTM Fiesta轎車的后擾流板。 Iveco卡車駕駛室的高頂采用RTM法成型,由意大利的Pianfei IPA的Mondovi廠制造。車頂總成的總面積為6m2,重量為45kg,樹脂為間苯樹脂,采用的預成型材料是熱成型連續(xù)纖維氈。 SP5A駕駛室頂由Polymer Engineering 公司用RTM方法生產(chǎn),配套服務于ERF 卡車,面積達到12m2。 材料:Class 1 BS 476 Part 7聚酯樹脂; 結(jié)構(gòu):6個獨立泡沫嵌件、攻絲嵌件; 生產(chǎn)線:雙模具、雙工位的模具安裝系統(tǒng); 后加工:經(jīng)過計算機控制的多軸機器拋光后,進入噴涂車間。 巴西Technofibrac SA公司,廣泛采用低成本的RTM成型工藝生產(chǎn)大型卡車車頂、面罩,豪華客車及公共汽車前臉、后尾,鋪路車、油礦車車身、駕駛室總成等大型玻璃鋼車輛部件,為Buscar、Ford、Volkswagen、GM、Honda等許多世界知名的汽車公司配套,1998年達到年產(chǎn)2,200噸的生產(chǎn)批量。 意大利的Sistema用RTM工藝為為Iveco車型配套制造箱式貨車、卡車和教練車的車身、車頂,車頂最大達到14m2。他們認為,其優(yōu)點是具有較好的空氣動力學特性,在85km/h的車速下,減少空氣阻力20-25%。 Advanced technology transit bus(ATTB)公司使用FRP減輕自重、減少油耗和尾氣排放。由Metropolitan Transportation Authority(MTA)公司制造車體結(jié)構(gòu),比傳統(tǒng)的公共汽車減重達4000kg,傳統(tǒng)的公共汽車車體結(jié)構(gòu)由數(shù)千個部件組成,但ATTB只有4個部件,采用VARTM復合夾芯工藝制造,選用Dow Chemical 公司Derakane環(huán)氧乙烯基樹脂和PVC泡沫夾芯板,制造了包括:車頂、側(cè)板、底盤和側(cè)防撞板。 國內(nèi)代表性的RTM工藝汽車部件有北京玻鋼院生產(chǎn)的奧拓尾翼、半透明卡車遮陽罩、中國重汽“飛龍”卡車面罩、陜汽德御車型翼子板;北京玻璃鋼制品有限公司生產(chǎn)的北方奔馳導流罩、二汽非金屬零件公司生產(chǎn)的“猛士”車型的發(fā)動機罩等。
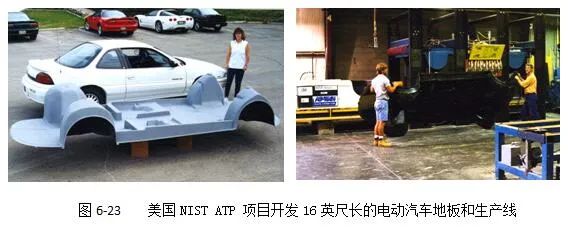
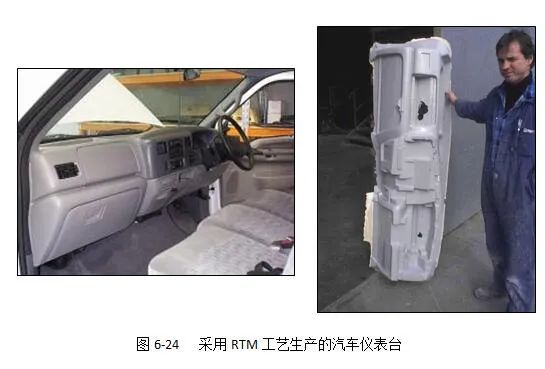
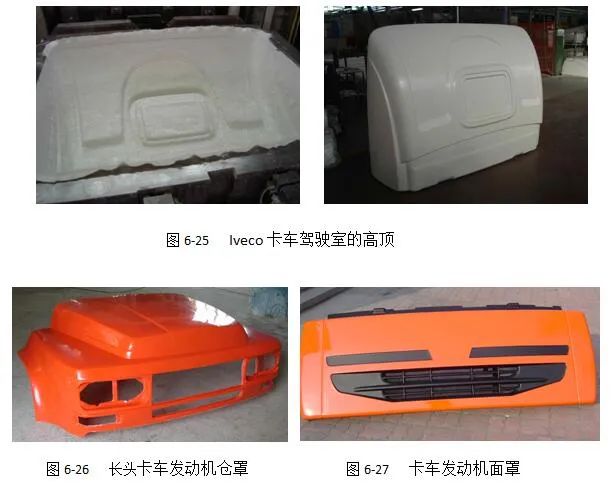
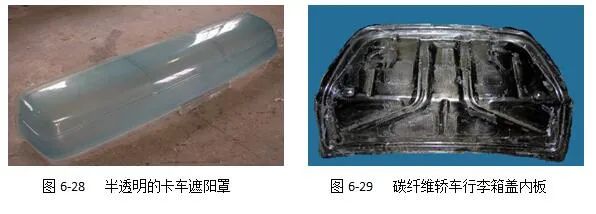
船用玻璃鋼部件的特點是面積大,一般多采用VARTM技術(shù)或SCRIMP工藝制造。目前在游艇制造方面應用非常多。SCRIMP工藝特別適合制造大型復雜結(jié)構(gòu)的部件,部件尺寸越大,成本優(yōu)勢越明顯。同時,一些嵌入件,如肋、加強筋和芯材都可以在成型是放入部件中一次成型。
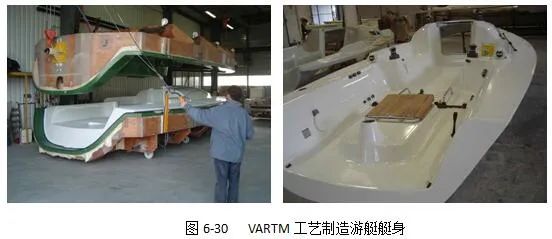
如下圖所示的公用電話亭外殼,產(chǎn)品重量12Kg,采用Light-RTM工藝環(huán)形生產(chǎn)線制造。生產(chǎn)線單模循環(huán)周期1小時,生產(chǎn)線有25個模具,日產(chǎn)量可以達到600件。
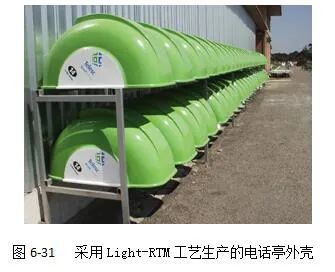
圖6-32為北京玻鋼院復合材料有限公司生產(chǎn)的RTM油站地下儲油罐井蓋,其特點是重量輕,承載能力高,最大可承載40噸,是比較有代表性的復雜夾芯加筋結(jié)構(gòu)整體成型產(chǎn)品。
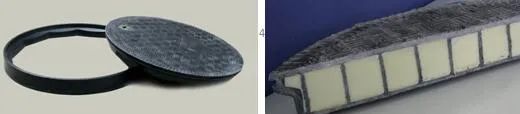
參考文獻
1、黃家康 岳紅軍 董永褀主編.復合材料成型技術(shù).北京:化學工業(yè)出版社.1999
2、(英)艾倫?哈珀 (中)董雨達編著.樹脂傳遞模塑技術(shù).哈爾濱:哈爾濱工業(yè)大學出版社.2002
3、倪愛清.復合材料液體模塑成型工藝中滲透率的研究〔D〕.武漢:武漢大學.2007
4、祝穎丹.LCM技術(shù)在線監(jiān)控體系的研究〔D〕.武漢:武漢理工大學.2007
5、王慶明.RTM復合材料模具研究〔D〕.北京:北京航空航天大學.2009
文章源自:微信公眾號 愛復材